Internal parts of the gearbox
All internal parts of the mechanism are made in the unwritten standard. This is good news in the event of a failure and for those who intend to upgrade the replica of the Edge series.
The pneumatic system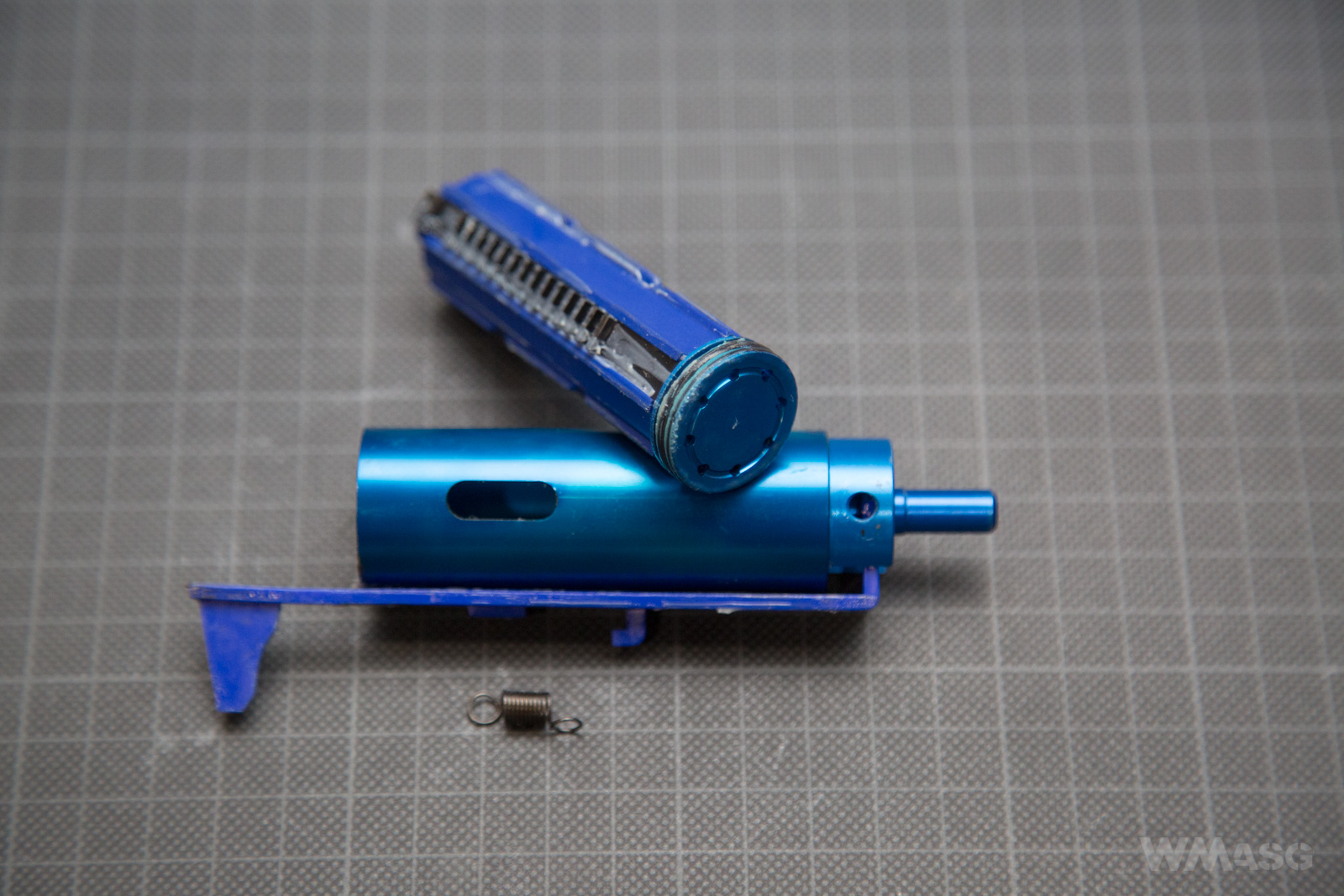
First the type 2 cylinder made of polished aluminum dyed in blue.
Next: an aluminum, double-sealed cylinder head with a thick bumper made of black rubber.
The piston has full-width steel teeth. The second tooth removed. The piston is different than the one used in the cheaper Core series.
The aluminum, double-sealed piston head has a full bearing. It is worth emphasizing that is has two o-rings.
Unfortunately, I will not show exactly the above-mentioned bearing because the thread was secured with glue and I did not want to struggle with it, I gave up, I could not unscrew the head. However, below you can see that the bearing is there.
The spring guide also has a bearing. The one used in the Core series looks very similar, but that one has no bearing.
A spring with regular coils. The second spring (an M90) that come with the replica also has regular coils.
A standard tappet plate with an equally standard spring.
And finally the nozzle. It is made of aluminum, dyed blue and sealed with an o-ring and has a length of 21.37 mm.
Mechanical parts
The replica has standard sintered steel gears. At first glance, they look the same as the gears used in other series of Specna Arms replicas (also Core). An anti-reversal latch also looks standard. A plastic delayer is attached to the sector gear.
The trigger lock and the cut-off lever are also standard.
The same goes for the trigger itself.
The electrical installation based on a typical trigger switch. Low resistance wires run in an insulation made from transparent plastic. They are moderately stiff. The swithc does not have additional external contacts surfaces that work only after the safety is switched off. It's a pity.
While we are at the electrical installation, I would like to direct your attention to two related matters. First of all, the installation is made according to a simplified scheme that was used some time ago when the MOSFET was mounted to the replica, but without replacing the wires. Then, an additional control wire coming from the system with the MOSFET to the conductor coming from the trigger switch to the "positive" motor terminal was added. Here we have such a variant. As a result, two standard thickness wires go from the MOSFET towards the trigger switch. As a rule, this is a risky solution, because the space around the motor shaft and its gear is quite small. In the Edge frame, the invented solution has been duplicated and a port has been cut out, thanks to which the wires have a little more space and are protected against being damaged by the motor.
Maybe it will be visible better here.
As for the way the installation is made, there is a better solution in every respect, both electrically and mechanically. For some reason Specna Arms did not decide to use this option. I mean, bringing two tiny signal wires to both terminals on the trigger switch, one of which goes out of the MOSFET and the other straight out of the positive pole of the battery. The wires can be as thin as possible. They only have a control current of very low intensity. The thick (standard) wire is going straight from the battery (it is connected to one of the control devices, e.g. in the replica's plug) to the "positive" motor terminal. Thanks to this, in a sensitive place we have two thin and flexible control wires and only one standard thickness wire. This solution is much more elegant, more reliable, and the risk of mechanical damage to the wires made by a gear on the motor shaft is even more limited.
The X-ASR MOSFET is a simple system that has a positive effect on the response of the trigger and the life of the trigger switch and the battery. Additionally, the module has been equipped with control procedures and an RGB diode, which informs about the correctness of operations or errors. The replica is accompanied by a short instruction, the size of the credit card, explaining the meaning of individual light signals and ways to remove defects.
GATE guarantees correct operation of the system only for springs up to M120. It's not much, but probably the system will also work with slightly harder springs.
The last part of the mechanism is the motor. According to the markings, it is a standard motor. Therefore, one should not expect from it a dizzying rate of fire.
To sum up the part regarding the replica's mechanism I have to say two things. First of all: the mechanism is exemplary assembled. The gears do not have the slightest lateral play and rotate without resistance.
Secondly: the way the motor is adjusted (settings relative to the bevel gear) is equally good. I have not met a factory made replica with such an efficiently and quietly operating mechanism.
If, however, I had to indicate some weak points of the factory assembly, I would say that that would be the electric installation, which we have already discussed, and too few lubricant on the gears. I would use a bit more.
On the next page: HopUp adjustment and the magazines